-
Five famous historical French figures who were exiled to Britain
From Voltaire to De Gaulle, we share the stories of five exiles who fled across the Channel
-
In France, do you know your porcherie from your pigeonnier?
These traditional structures have helped small-scale farmers source protein for hundreds of years
-
Neighbour who complained about noisy cockerel in France ordered to pay €3,500
The complainant said the animal, which has since died, crowed too loudly and too often
A French test drive with a difference...
Journalists are often offered the chance to test drive new cars but The Connexion's Brian McCulloch had a different opportunity - to get behind the wheel of a combine harvester in France. Here's his report...
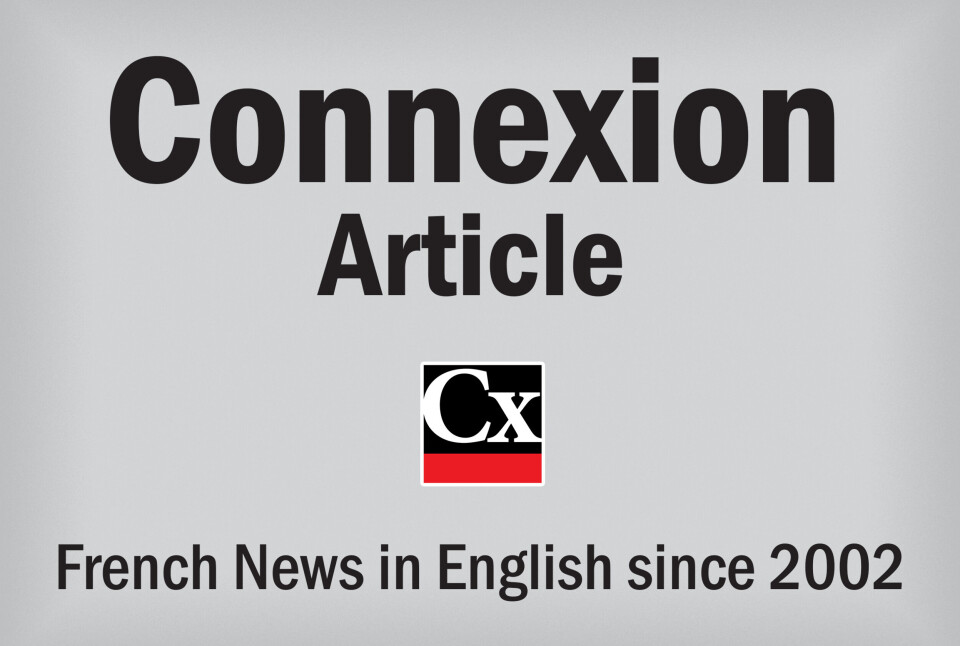
They are huge, noisy and dusty, and move like giant snails through the countryside from mid June, when the first barley is ripe, to December, for the last of the maize.
Modern combine harvesters weigh around 20 tonnes, have diesel engines of up to 600HP and do in half a day work which once took a fortnight.
And although they seem not to have changed much from the outside, French harvesters are now leaders in Europe in the use of GPS technology, with drivers of modern machines cutting the first row in a field and then taking their hands off the wheel and throttle.
“They do not just sit back and listen to the music, because without the driving part they are able to spend more time monitoring how the threshing and cutting of the straw is doing,” Julien Saint Laurent, of John Deere France, told Connexion.
France is one of the largest markets for the machines in Europe, and has been so for 40 years, so now it is possible to pick up ancient second-hand machines with manual gears and three metre wide cuts for as little as €2,000 … or you can pay 100 times as much for a new, 10 metre cut machine where almost everything is automated.
For such large machines they are surprisingly nimble, at least if they were produced in the last 15 years.
Power steering to the rear wheels means that every last stalk in the corner can be cut, and hydraulic suspension means the bumps in the field do not shake the driver and the machine can be tilted to mow crops on a slope.
In a quick go in the driver’s seat, under close supervision, and with the GPS not engaged, Connexion's Brian McCulloch found the combine very simple to drive, with hydrostatic gearboxes, as found on upmarket lawnmowers.
The main control when in the fields is a joystick controlled by the right hand. Push forward the machine goes forward, push back it goes back. Reversing is not something for the faint of heart, as rear visibility is limited to two wing mirrors - though, increasingly, rear-view cameras help.
Front, down and side visibility, by contrast, is excellent, as in a helicopter - and legend has it that people who get sea-sick also get combine sick after five minutes.
The joystick also has buttons to control the height of the blades, the speed and spacing of the thresher and the speed of the sieves and screws which handle the grain before it flows into a big tank behind the driver, fitted with a window so he or she can see how things are going.
“All our new machines now are sold with the equipment ready to be linked to GPS units if the farmer wants them,” said Mr Saint Laurent.
“They cost around €6,000 and pay for themselves, usually in the first year because of the increased efficiency in keeping a constant speed and turning efficiently at the end of the field.”
Official figures say GPS systems increase production by 10%, but Mr Saint Laurent said the actual results can be higher, especially on smaller farms which do not employ specialist drivers.
The actual GPS units are mobile and can be moved from the tractor, where they are used for planting, and spraying, to the harvester, with the field's dimensions and the position of rows of crops in the memory.
“The next moves will not be to get rid of the driver completely,” said Mr Saint Laurent.
“Instead we will probably see significant improvements in how the grains are threshed and the driver will have a key role. Where there are two or more machines now, the farmer can monitor on his smartphone and send the settings from that machine to the other one, where the driver just needs to push a button to accept them. That, too, is an area which will develop.”
At the front is a rotary comb which lines up the stalks of the crop to be cut, ready for the scissoring blades of the cutter.
Combs and cutters detach from the machine and are towed on trailers behind it on public roads and different front modules are used for different crops.
How wide the cutter is usually depends on the age of the machine – 35-year-old models, still seen in the fields of France, usually cut three metres at a time, new machines up to 10 metres.
Cut stalks and grain heads are fed by rotating screws to a central tunnel and then up an elevator and into a threshing drum where the grains are separated from the stalks by being beaten by pales, before being directed to the first of a series of sieves, similar to those builders use to sieve sand.
Vibrating to and fro and backwards and forwards the sieves shake the grain from the stalks and on to an Archimedes screw which takes it to a tank, capable of holding five tonnes at a time. Blowing over the sieves, air from a powerful fan further separates dust and straw from the grain – and also accounts for much of the deafening noise the machine makes outside.
In the cabin, modern machines are scarcely more noisy than a car.
Another screw system takes the stalks and chaff and ejects it out the back in long lines, ready for the bailer to follow, if the stalks are being used as straw, or chops it up and sprays it, if the stalks are to be left on the ground.
Every 10 minutes or so the machine has to disgorge its grain, usually into new steel trailers matched to the larger tractors on the farm, capable of carrying 10 tonnes a time.
Driving these huge machines are farmers, their offspring and workers, sometimes putting in 12 hour days - starting at 11h.
While it is not physical work, you need to concentrate to cut in the most efficient way, and avoid the monster machine knocking down houses, trees or even the grain tractors next to it.
The 11h start is to allow the dew to dry off. The price at the grain silo depends on the weight of grain delivered, with a negative calculation for the farmer if the humidity of the grain exceeds given limits.
Similarly the dew point in the evening determines when the giant machines are left to cool down.
Lines to be cut have usually been worked out generations before (combines became common on smaller French farms in the mid 1960s), and the same patterns usually repeat themselves year after year.
Most of the cabins have the driver sitting in splendid isolation with a jump seat for the times when there are visitors.
Almost all have a decent air-conditioning system, essential for what is essentially a three-sided glass house moving through baking hot afternoons.
Stay informed:
Sign up to our free weekly e-newsletter
Subscribe to access all our online articles and receive our printed monthly newspaper The Connexion at your home. News analysis, features and practical help for English-speakers in France