-
Breton name bowls: 'People are no longer interested in the traditional craft'
These bowls have become a staple of French cabinets and breakfast tables, but how are they really made?
-
Five famous historical French figures who were exiled to Britain
From Voltaire to De Gaulle, we share the stories of five exiles who fled across the Channel
-
Ski resort in French Alps to close due to lack of snow and funding cuts
Local officials have announced the closure of the Alpe du Grand Serre station in Isère, halting plans to keep it open year-round
Craftspeople in France - ski maker
The artisans keeping alive proud French ski traditions
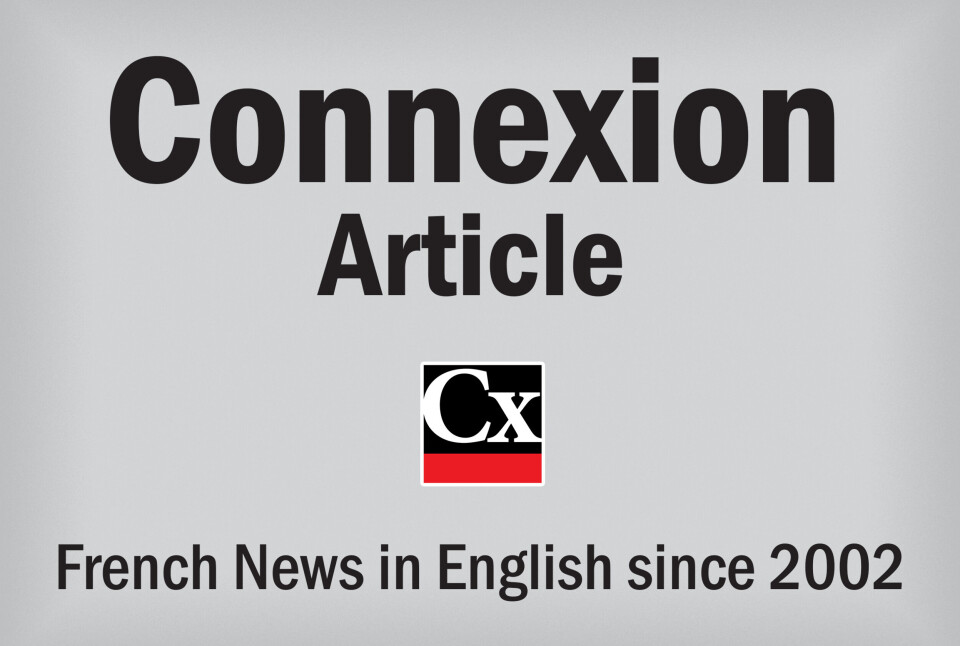
Around half of the world’s skis were made in France in the 1980s, but many of the main manufacturers have now moved to countries where labour is cheaper.
There are, though, a growing number of small French artisanal companies where skis are made by hand.
One is La Fabrique du Ski, based at Villard-de-Lans, Isère, which has a range of 14 models of ski (fabriqueduski.com).
In the workshops, three craftsmen make 15 skis a week, each taking six to eight hours to make.
Their hallmark is the bamboo they are made with and the time the company devotes to research and development, so that design and performance are constantly reassessed and upgraded.
The company was created by Christian Alary in 2013. He was brought up in the mountains, skied from a very young age, trained as a mechanical engineer and then spent years working in the ski industry.
“There is no formal training scheme to learn how to make skis – you have to learn by working with others who make them,” he said.
He said he has good memories of his time in the ski industry, particularly learning and working with winter sports specialist Rossignol.
During that time, he developed ideas of his own that he was keen to put into practice: “Most skis are made in moulds dedicated to specific models, which are costly to produce, so that you need to make between 5,000 and 10,000 skis to make them cost-effective.
“I developed a system, which I have patented, which allows each pair of skis to be made individually, so that you can make as many or as few as you like of each model.
“This means I can be much more flexible with my designs and it is much quicker to turn a new idea into an actual pair of skis.
“I have been able to have an idea one evening, and make it and test it out by the end of the next day.
“This method also means that instead of putting money into creating a mould, we can use it to purchase top quality raw materials.”
Each ski is a multi-layered sandwich of between 20 and 25 elements.
In production, the first stage is to prepare each layer.
Bamboo from Asia, which is processed in Slovenia to meet the company’s specific needs, is used because it can absorb shocks easily and so, La Fabrique claims, produces a ski which is stable and performs well, whatever the snow conditions.
Other materials include carbon and glass fibre, P-Tex – a type of polyethylene that is regularly used in snow sports equipment – as well as plastic and aluminium.
The company’s latest ski, “Sillage”, launched this winter, also uses Titanal, an alloy of aluminium, copper, magnesium and zinc, used in the highest-grade skis and snowboards, as well as bamboo, carbon and even slate.
It is a ski Mr Alary is particularly proud of, which, he says, brings the pleasure of the top sporting skis to a wider public.
First, the soles are cut using a digital cutter which takes its information directly from a computer design.
The metal ski edges are added and all the other layers are cut to size, either by machine, or more low-tech scissors.
In the second stage, the layers are stuck together and then put in a vacuum mould to give them the required curve.
Thirdly, and this is the procedure which takes up about half of the time, the finishing stage, where the skis are trimmed, sanded and polished.
Mr Alary said there are many factors to take into account when making skis: “The geometry, the rigidity, the position of the ski on the foot, etc. The most important element is to test the design you make on the computer out on the snow.
“To achieve a final design, we have far more failures than successes.
“The result I am proudest of is my “Où tu veux quand tu veux” model, which can be used for all type of mountain terrain, whether the snow is powdery or hard.
“It needed a great deal of creativity and experimentation to come up with something that would really work.”
Mr Alary spends about 80% of his time in production.
It is a job which is both manual and intellectual: “Because our output is small, and because of my patented method of production, we do have the luxury of more design time than most businesses and this is what makes it so satisfying, to be able to create and develop the product.”
The skis are more expensive than an off-the-shelf pair from Décathlon, which start from around €130, but Mr Alary says it is impossible to make them cheaper.
He said that, with prices starting from €620 a pair, they are not as expensive as many other handmade skis: “I want to make them as accessible as possible and to be used by all levels of skier, from beginner to sportsperson.
“I am proud they are Made in France, but I do not want to sell them with that label alone.
“I want people to buy them because they are good skis.”