-
Podcasts and exhibitions: four French cultural ideas
Find inspiration for outings and a way to deepen your knowledge of France
-
Uncovering France's Easter Island statues
There are five statues in various locations across France
-
Breton name bowls: 'People are no longer interested in the traditional craft'
These bowls have become a staple of French cabinets and breakfast tables, but how are they really made?
Makhilas: Discover traditional Basque walking sticks made in France
The sticks have been made by the same family for seven generations, with the 94-year-old grandfather of the family still lending a hand
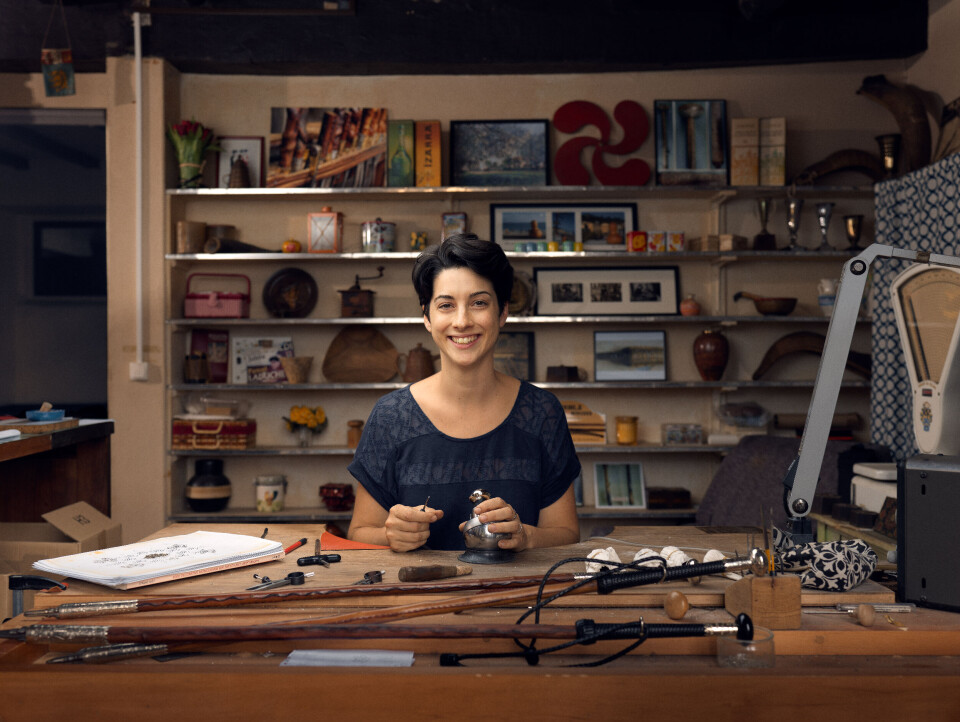
The Bergara family has been making traditional Basque walking sticks for more than seven generations.
Records show they were being made by the same family in the 18th century.
Now the company, whose Ainciart Bergara workshops are at Larressore, Pyrénées-Atlantiques, is run by Liza Bergara, who has taken over from her mother Nicole.
Her 94-year-old grandfather Charles continues to work with them.
The workshop (makhila.com) has had many prestigious orders over the years from big names in the world of politics, religion and showbusiness, including all French presidents since Charles de Gaulle, Pope Jean Paul II, Sean Penn and French actor Jean Dujardin.
However, these beautifully crafted objects are not just for celebrities but are intended to be used as an everyday walking stick.
Each one is made to suit the morphology and tastes of the person it is designed for.
“In the past, every region in every country had their own style of walking sticks,” said Ms Bergara. “They were such a part of daily life in the Basque country that there are few written descriptions until the 19th century, when people began to travel and visitors to the region began to admire and to write about them.
“We have maintained the tradition, with a few subtle changes over the generations to suit each era.”
Makhilas are made from medlar wood, with a metal sleeve at the top made out of either silver, bronze or nickel silver, according to taste and budget, leather decorations and wrist strap, and a domed knob as a handle.
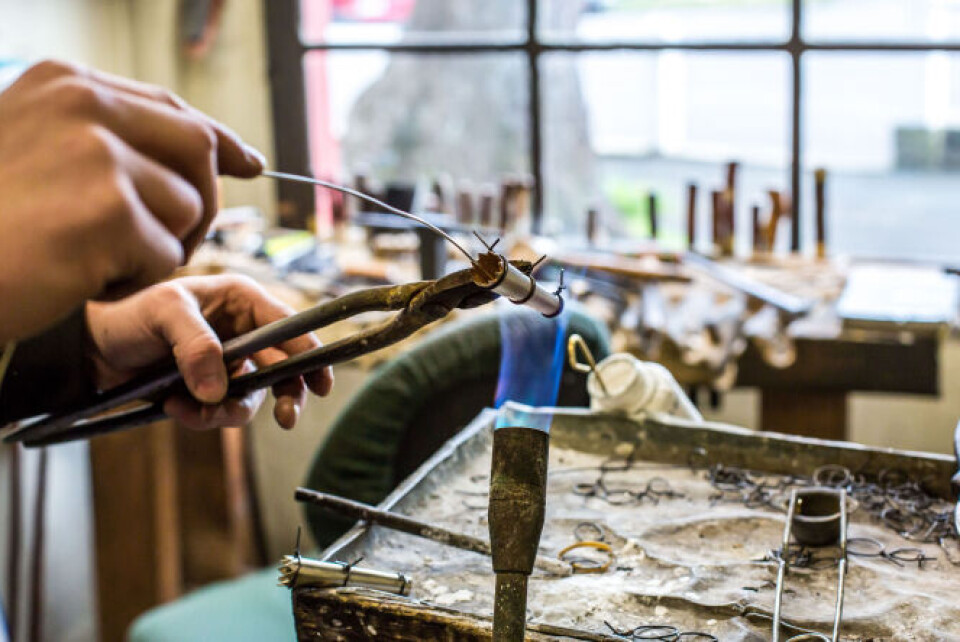
Brazing the metal collar to fix it. Pic: CEN photographie / provided by interviewee
Ms Bergara says there are several steps to making them, requiring many different skills.
“The medlar has always been used because it is both strong and flexible. It grows very slowly and it takes about 10 years for a branch to grow to the required diameter.
“We start decorating the future cane while it is still growing on the tree by making shallow marks with a knife along its length, perhaps in waves or a broken line. It takes great skill to know just how deep to cut.
“The branch is left on the tree for a further six months for the marks to heal, before it is cut and then passed through a wood-fired oven at a high temperature to take off the bark.
“We are left with a white wood. Only the best specimens are kept. They are coloured using a secret recipe passed down the generations and, depending on the reaction with the wood, the result is always different, giving a choice from beige to dark brown.
“The sticks are stored in our attic for up to 10 years until they are ready to be chosen and turned into a makhila.”
The metal part is cut to the size of the chosen stick and formed into a collar by applying heat to braze it and hold it together. Then the detailed decoration work begins. It is engraved into the metal by punching it in with tiny chisels.
The motifs are traditional, but applied in different combinations on each makhila. Fern and the Basque cross are signature motifs of the workshop.
“I engrave the initials of the customer on the domed knob and sometimes a design if the client asks for one,” said Ms Bergara. “It is very precise work and you have to go slowly and carefully. If it is a complicated coat of arms, it might take me half a day.”
Some of the canes have leather plaited around the cane between the wood and the metal. The strong leather comes from a Basque tannery and is plaited in a particular way, which is another well-guarded secret.
It is very technical and needs hours of training. The wrist strap is also made of four strands of plaited leather.
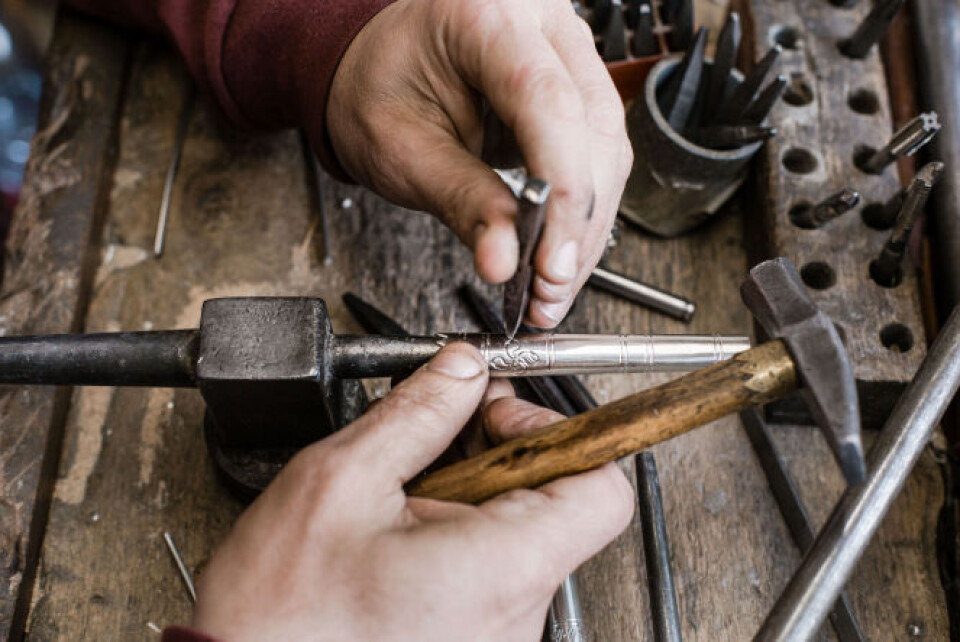
Punching in the design with small chisels. Pic: CEN photographie / provided by interviewee
“There are seven artisans in the workshop, including myself,” said Ms Bergara.
“Each makhila passes through the hands of four to six different people and takes around 20 hours to make.
“Prices start from €350 for the basic model, and reflect the amount of work and savoir-faire that goes into each one, which is always tailor-made to the requirements of the client.
“We make around 800 a year. There is a 20-month waiting list for orders.”
There is nowhere to learn the unique skills required to make a makhila, other than in their workshops, though Ms Bergara did train as an engraver at the fine arts and crafts school in Paris, Ecole Boulle, because she was living there at the time, when one of the employees was due to retire.
It meant she had to agree to join the family business. “It takes years to be fully at ease with the skills. In recent years, four people have retired, so younger employees, including myself, are still learning.
“It means we cannot go quite as quickly as when nearly everyone here had 40 years’ experience, but we accept that and do not try to rush. The important factor is to make each walking stick as carefully and as perfectly as possible.”
Related stories:
Art of trimmings: The artisans who supplied French and Monaco royals
The only company making wooden jigsaws by hand in Europe is French